History of FIBC
Home » Knowledge Center » History of FIBC
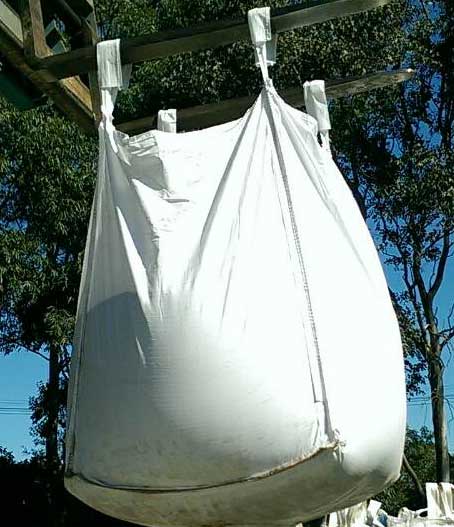
History of FIBC
Flexible intermediate bulk containers (FIBC) or bulk bag is characterised as an intermediate mass holder, having a body made of adaptable texture (polypropylene), which
– Cannot be hand-operated when filled
– Suitable for shipment of solid material (in powder, flake, granular form).
– Does not need to be packaged more.
– Should be lifted from the top as the design intends, by means of permanently attached features (lift loops or straps).
Flexible intermediate bulk containers (FIBCs) also known commonly as ‘bulk bags’ were first produced in the late 1950s or early 1960s. The first FIBCs were fabricated with durable PVC coated nylon or polyester which were sewn together to form the bag.
The bulk bags were made with joined light slings around the container, or fastened to a specially made pallet or a lifting machine that the container was placed on. The handling devices permitted the container to be loaded from the top and emptied from the bottom.
FIBCs were first manufactured in the United States, Europe and Japan during the late 1950s to the early 1960s. However, there is much dispute as to which country produced it first. The quick development in Europe in the production of FIBCs happened in the mid 1970s amid the oil crisis. The oil-manufacturing building program nations required vast amounts of cement. The high demand for cement was transported in FIBCs at the rate of 30,000-50,000 metric tons every week from Northern Europe, Spain, and Italy to the Middle East.
The increasing demand for bulk bags in Europe developed faster than the USA until 1994, when the US Department of Transportation (DOT) consented to concede exceptions for the shipment of dangerous items in FIBCs. Performance and quality standards for FIBCs were set up and issued by the Chemical
Packaging Committee of the Packaging Institute, USA. These expectations were utilizedto acquire exemptions until DOT included adaptable holders with alternate kinds of IBCs in the Title CFR 49 for hazardous products.
FIBCs offer features that are distinctive. It can be folded flat for shipment. The weight of of a bulk bag offers low package: product weight ratio. The price of bulk bags are compared with other forms of packaging as it is normally used without pallets. They are convenient to store and deal with in warehouses with standard hardware. When shipping overseas by boat, the bulk bags are stacked in groups with up to 14 bulk bags on a spreader bar and are dispatched as bulk mass.
The required filled diameter of a bulk bag is 114-122cm approximately. It is designed to fit 2 across in a truck or shipping container. Design holders are made to meet explicit necessities of the user.
FIBCs are produced to meet specific requirements of the users. The height of the container, the diameter, and length of the spouts, coated or uncoated texture and whether a polyethylene liner is required will be indicated by the type of item that will be transported.
When unsafe items are transported in FIBCs, the UN mark should be imprinted on the body of the container.
In the US, the manufacturer or a third party lab, may affirm the container according to the rules and regulations in part 178 of the Title 49 CFR. Every single country need a third party lab to certify the container.
FIBCs containing non-risky or unmanageable products when shipped from the US must have performance testing accreditation if bound for a nation that requires performance standards for bulk bags.